The Manufacturing Process
How Are Our Custom Weed Bags Made?
At BudPouch.com, we use a meticulous, step-by-step process to create high-quality custom weed bags. Our manufacturing process involves cutting-edge technology and top-grade materials to ensure durability, safety, and customization for every order. Below is a breakdown of each phase of our manufacturing process:
1
Raw Material (Mother Rolls) – The Foundation
Our custom weed bags start with large format bobbins of raw materials, known as mother rolls. These rolls serve as the foundation for our packaging. We use a variety of materials, depending on the specific requirements of the customer:
- MOPP (Metalized Oriented Polypropylene)
- PE (Polyethylene)
- PET (Polyester)
- Other Materials: Custom materials upon request
These raw materials are carefully selected for their strength, flexibility, and suitability for the specific packaging needs, ensuring that our custom weed bags perform at the highest standard.
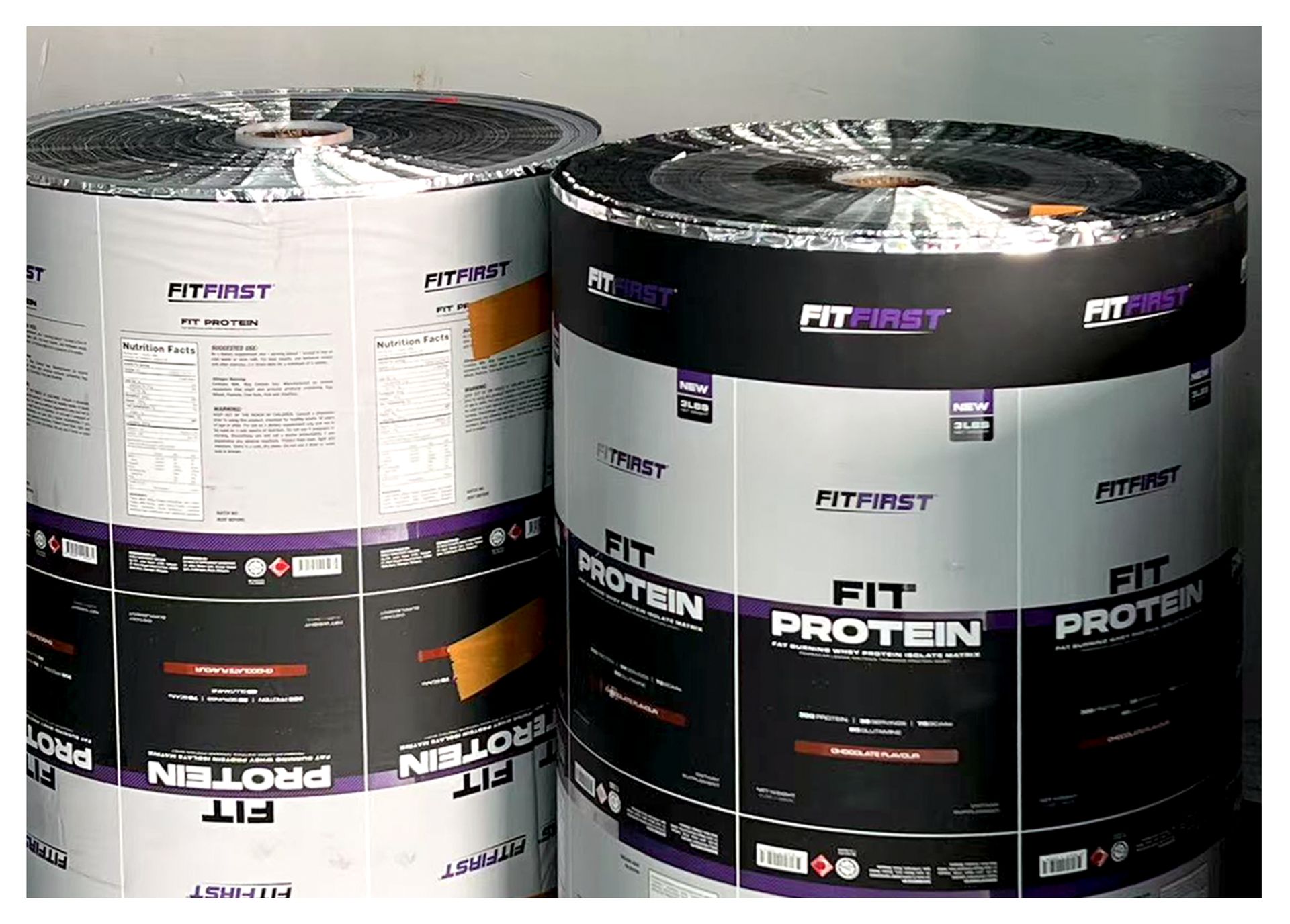
2
Printing on the Outer Layer
Once the raw materials are prepared, we move to the printing phase. This involves printing on the outer layer of the material, which is typically PET or MOPP. We use a lithographic printing press for this process, allowing for precise, high-quality full-color prints that bring your brand's design to life.
The printing process ensures that your logo, artwork, and branding are displayed with vibrant clarity, and that the design is long-lasting, even under typical handling conditions.
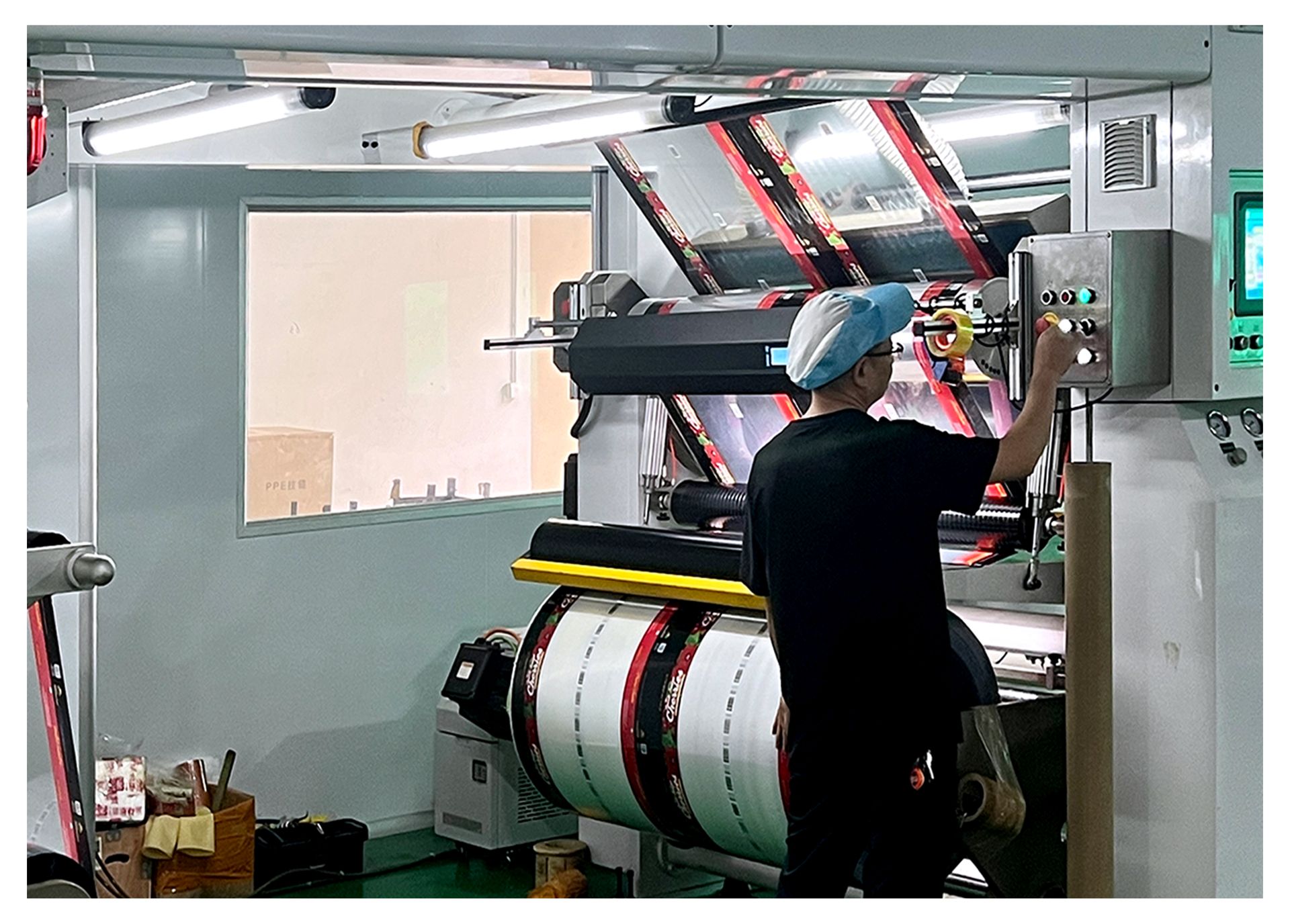
3
Bonding the Layers Together
After printing, the next step is bonding the layers together. In this phase, we merge the printed outer layer with the inner layer (usually PE) to form the structure of the custom weed bag. The bonding process creates a consistent thickness, typically 130 microns, but we can customize the thickness to meet your specific needs.
The bonded layers form the strength and durability of the custom weed bag, ensuring that it is sturdy enough to hold the flower and prevent any leakage or damage.
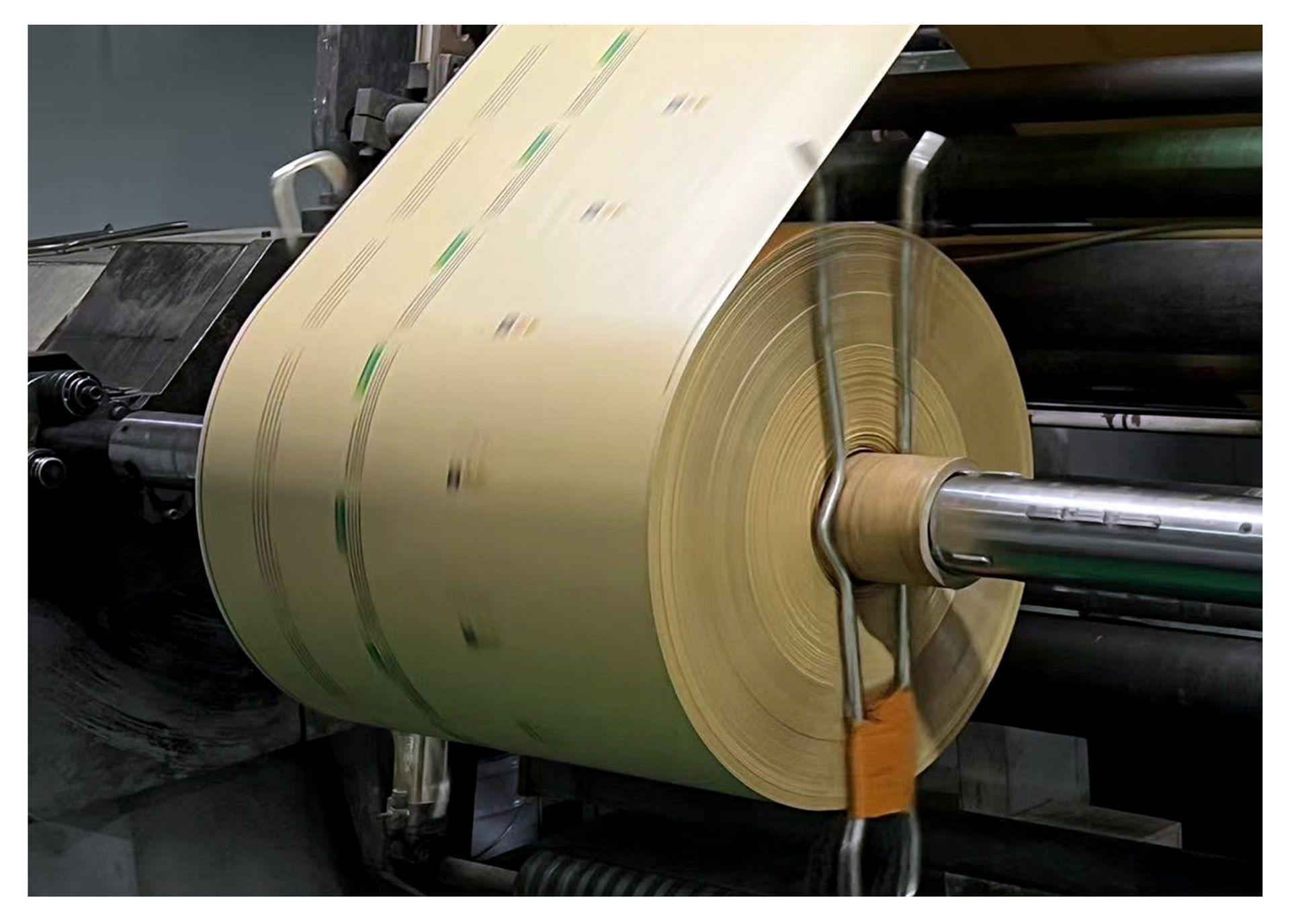
4
Bag Forming and Sealing
After the bonding, the material is loaded onto our bag-making machine, where it undergoes the final steps of the process. The custom weed bag is formed from the raw material into the shape of the final bag, cutting and sealing the edges to create a perfect, finished product.
This step also includes the addition of essential features, such as:
- Male to Female Zippers: If required, we can add zippers to make the bags re-sealable. This feature is especially important for keeping your product fresh and preventing odor escape.
- Sealing the Bag: The custom weed bag is sealed at the edges using precision cutters, ensuring it is secure and reliable.
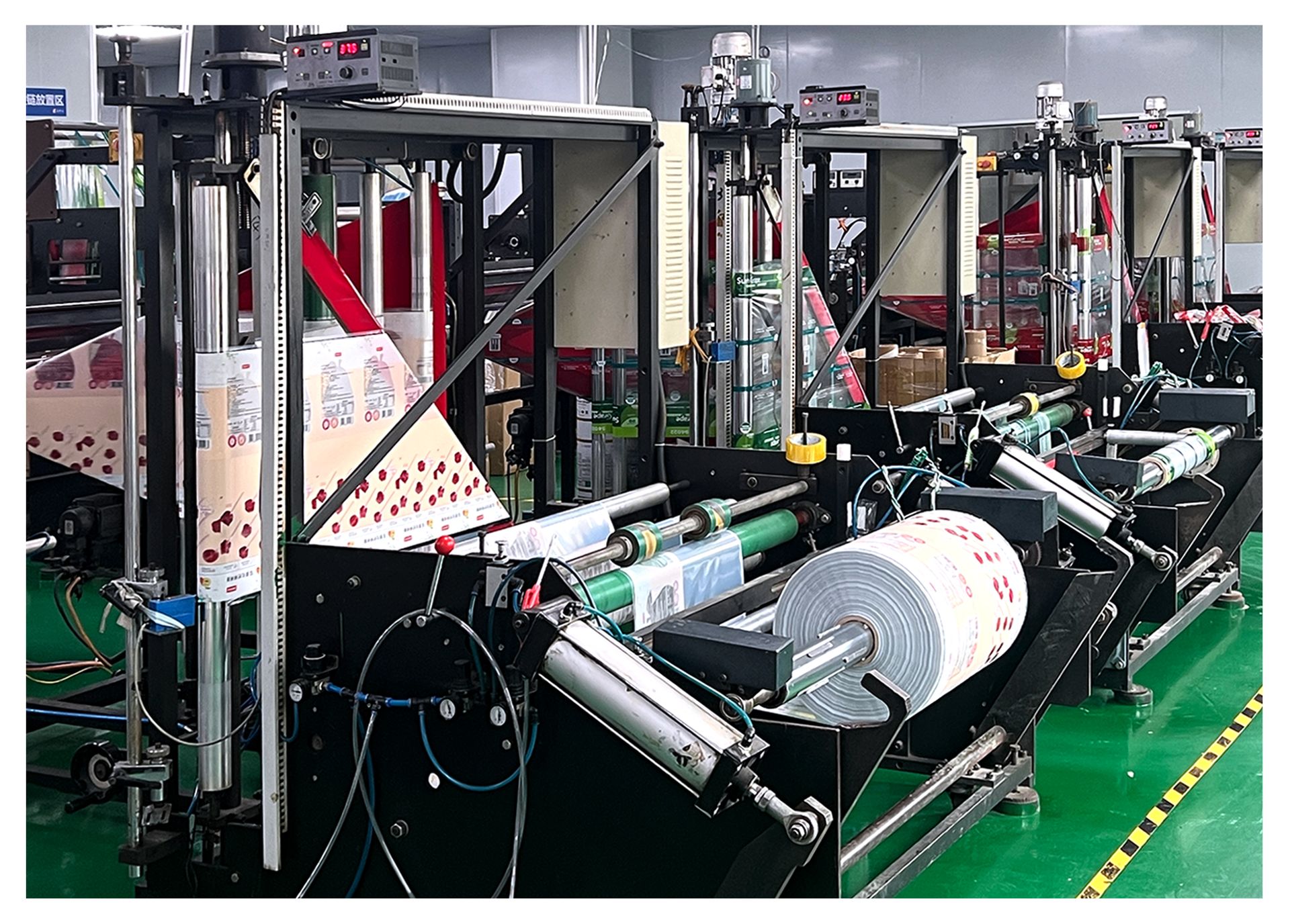
Summary of the Manufacturing Process
This step-by-step process ensures that every custom weed bag is crafted with precision and quality, meeting both your aesthetic and functional requirements. Whether you need a simple, classic design or a unique custom shape, we can deliver it all.
- Raw Material (Mother Rolls): Large format bobbins of materials like MOPP, PE, PET.
- Printing: Flexographic printing on the outer layer for high-quality branding.
- Bonding: Merging layers to create the required micron thickness (e.g., 130 microns).
- Bag Forming and Sealing: The material is transformed into the final bag shape, with added features like zippers.
Contact Us for Custom Orders
Have a custom packaging need? Reach out to us today and we’ll guide you through the process to create the perfect custom weed bags for your brand.